Suche
Ergebnisrelevanz: 1%
zurück zum SuchergebnisProduktion
Unser globales, markenübergreifendes Produktionsnetzwerk stellt die Prozesse vom Lieferanten zur Fabrik und Montagelinie sowie aus der Fabrik zum Handel und zum Kunden sicher. Eine dauerhafte Effizienz ist Voraussetzung für unsere Wettbewerbsfähigkeit. Mit ganzheitlichen Optimierungen, zukunftsgerichteten Innovationen, flexiblen Lieferströmen und Strukturen sowie einer agilen Mannschaft begegnen wir den Herausforderungen der Zukunft. Im Geschäftsjahr 2019 lag die weltweite Fahrzeugfertigung mit 10,8 Mio. Einheiten leicht unter dem Vorjahreswert. Trotz anhaltend schwieriger Rahmenbedingungen in vielen Märkten nahm die Produktivität im Vergleich zum Vorjahr um rund 4,0 % zu.
Produktionsstrategie „Intelligent vernetzt“
Die Produktion unterstützt die weiterentwickelte Konzernstrategie TOGETHER 2025+ mit ihrer Funktionalbereichsstrategie „Intelligent vernetzt“. Durch die intelligente Vernetzung von Menschen, Marken und Maschinen wollen wir die Kräfte und Potenziale unserer weltweiten Fertigung und Logistik bündeln und dadurch Synergien erschließen. Die Leitplanken sind unsere vier strategischen Zielfelder:
- Wandlungsfähiges Produktionsnetzwerk
- Effiziente Produktion
- Intelligente Produktionsprozesse
- Zukunftsfähige Produktionsarbeit
Mit geschäftsbereichsspezifischen Initiativen haben wir inhaltliche Cluster gebildet, in denen kompetenzstarke Teams die für die Produktion im Konzern relevanten strategischen Themen bearbeiten. Die wettbewerbsfähige Gestaltung unseres weltweiten Produktionsnetzwerks, die Reduzierung und der Ausgleich von Umweltbelastungen entlang des Produktionsprozesses sind ebenso Beispiele wie die Digitalisierung mit ihren Auswirkungen auf Produktions- und Arbeitsprozesse sowie auf die Zusammenarbeit. Übergreifendes Ziel ist es, die Produktivität und die Profitabilität zu steigern.
Mit der Produktionsstrategie haben wir die Basis für eine erfolgreiche und nachhaltige Weiterentwicklung unserer Produktion geschaffen. Mit regelmäßigen Reviews stellen wir sicher, dass wir unsere Aktivitäten laufend an den aktuellen Herausforderungen ausrichten.
Globales Produktionsnetzwerk
Mit zwölf Marken und 124 Produktionsstandorten sind einheitliche Standards für Produktkonzepte, Anlagen, Betriebsmittel und Fertigungsprozesse wichtige Bestandteile der zukunftsorientierten Fertigung. Diese Standards ermöglichen es uns, Synergien zu erzielen, flexibel auf Marktanforderungen zu reagieren, ein flexibles Produktionsnetzwerk optimal auszulasten sowie Mehrmarkenstandorte zu realisieren. Aktuell sind bereits knapp die Hälfte der 45 Pkw-Standorte Mehrmarkenstandorte. Das Musterbeispiel im Konzern bleibt weiterhin der Standort Bratislava: Hier werden Fahrzeuge der Marken Volkswagen Pkw, Audi, Porsche, SEAT und ŠKODA produziert.
Der Volkswagen Konzern hat sich zum Ziel gesetzt, bis 2025 ein weltweit führender Anbieter batterieelektrischer Fahrzeuge zu werden. Grundlage hierfür ist die Einführung des Modularen E-Antriebs-Baukastens (MEB). Mit ihm ergänzen wir unser Angebotsportfolio um weitere batterieelektrische Fahrzeuge. Seit 2019 werden in Zwickau, dem ersten Elektrostandort des Volkswagen Konzerns, batterieelektrische Fahrzeuge auf Basis des MEB gefertigt.
Um Mehrmarkenprojekte und Elektromobilität in Verbindung mit bestehenden Konzepten wirtschaftlich zu gestalten, ist es wichtig, die Fertigung höchst flexibel und effizient auszurichten. Außerdem ist die maximale Nutzung von Synergiepotenzialen ein entscheidender Faktor für den Erfolg künftiger Fahrzeugprojekte. Der Einsatz von gleichen Teilen, Konzepten sowie Fertigungsprozessen ermöglicht die Reduzierung von Investitionen und die Chance, vorhandene Kapazitäten besser auslasten zu können. Zukünftig werden elektrifizierte Fahrzeugprojekte an Mehrmarkenstandorten wie zum Beispiel in Zwickau und im chinesischen Anting hinzukommen.
Wir entwickeln unsere Produktionskonzepte stetig weiter und richten sie auf neue Technologien aus. Dabei dient der in der Strategie verankerte Targetierungsprozess der Realisierung von ambitionierten Zielen in den einzelnen Projekten.
Produktionsstandorte
Das Produktionsnetzwerk des Volkswagen Konzerns umfasst 124 Standorte, an denen Pkw, Nutzfahrzeuge und Motorräder sowie Aggregate und Komponenten gefertigt werden.
Mit 72 Standorten bleibt Europa unsere wichtigste Produktionsregion für die Fertigung von Fahrzeugen und Komponenten. Allein in Deutschland befinden sich 28 Standorte. Die Region Asien-Pazifik hat 33 Standorte. In Nordamerika sind es sechs und in Südamerika neun Standorte. In Afrika betreibt der Konzern vier Standorte.
Im Jahr 2019 haben wir 89 Produktionsanläufe durchgeführt, davon waren 29 neue Produkte beziehungsweise Produktnachfolger sowie 60 Produktaufwertungen oder Derivate.
Die Auslastung der Standorte im Produktionsnetzwerk des Volkswagen Konzerns wird durch die Belieferung mit Teilesätzen als Completely-Knocked-Down (CKD)-Standort weiter gestärkt.
FAHRZEUGPRODUKTIONSSTANDORTE DES VOLKSWAGEN KONZERNS
Anteil an der Gesamtproduktion 2019 in Prozent
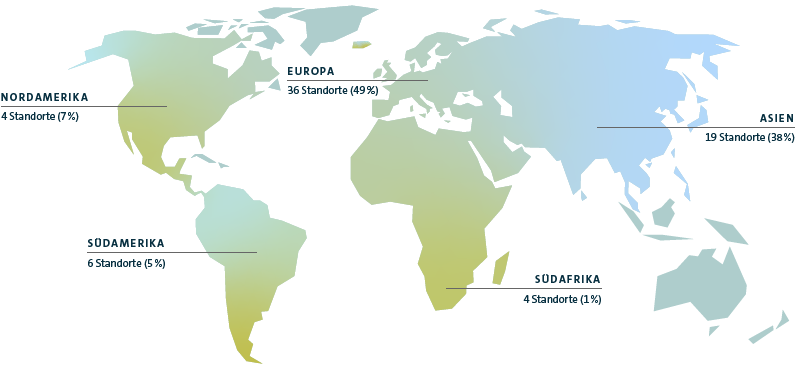
Das Konzern-Produktionssystem
Das Konzern-Produktionssystem verfolgt das Ziel, die Abläufe an allen Standorten der Marken und Regionen kontinuierlich und nachhaltig zu verbessern. Um exzellente Prozesse in der Produktion und im produktionsnahen Umfeld zu erreichen, ist das Konzern-Produktionssystem der zentrale Baustein, welchen wir stetig festigen und dessen Durchdringungsgrad wir erhöhen.
Unabdingbar sind dabei die Themen Führung sowie Verantwortung des Einzelnen, welche durch den wertschätzenden Umgang miteinander sichtbar werden und Teil unserer Kultur sind.
Die optimale Auslastung unserer Fabriken ermöglicht, Produkte mit hoher Qualität und hohem Kundennutzen zu wettbewerbsfähigen Kosten zu fertigen. Gewährleistet wird dies durch die frühzeitige Standardisierung von Fertigungsprozessen und Betriebsmitteln. Grundlage für die Standardisierung ist die sogenannte Konzeptgleichheit: Sie sorgt dafür, dass in den Entwicklungs- und Produktionsbereichen der Marken gemeinsame Konstruktionsprinzipien, Fügetechniken und Fügefolgen, aber auch Verbau- und Anbindungskonzepte angewandt werden. Die Konzeptgleichheit ist das Fundament für effiziente Logistik- und Fertigungsprozesse.
Neue Technologien und Roadmap Digitalisierung
Der 3-D-Druck ist nach wie vor eine der Schlüsseltechnologien von Industrie 4.0 und der Digitalisierung der automobilen Wertschöpfungskette. Er wird in ausgewählten Standorten im Volkswagen Konzern sowohl für die Bauteile- als auch für die Betriebsmittelherstellung erfolgreich eingesetzt. Das Verfahren eröffnet in den Bereichen Entwicklung, Design und Produktion völlig neue Möglichkeiten. Aufgrund des digitalen Charakters der Technologie, die keinerlei Werkzeuge benötigt, lassen sich Bauteile und Betriebsmittel flexibel und direkt aus digitalen Zeichnungen umsetzen sowie gänzlich neue Designs und Bauteilgeometrien verwirklichen.
Entwicklungen in Richtung Großserienanwendungen im Automobilbau lassen für die Zukunft noch erhebliche Potenziale erkennen. Volkswagen nutzt hier durch die enge Zusammenarbeit seiner Marken die Vielfalt des Konzerns und arbeitet mit führenden Technologieanbietern und Forschungseinrichtungen zusammen. Neben den neuen Technologien ist in den nächsten Jahren die Umstellung der IT-Architektur auf eine cloudbasierte Plattformlösung die Kernaufgabe auf dem Weg zur digitalisierten Fertigung. Der Volkswagen Konzern nähert sich so dem Zukunftsprojekt Industrie 4.0. Die cloudbasierte Plattform mit ihrem vereinfachten Datenaustausch ist eine entscheidende Voraussetzung, um Innovationen schnell und standortübergreifend bereitzustellen. Beispiele sind intelligente Robotik oder Funktionen der Datenanalytik, um werksübergreifende Prozesse zu analysieren und zu vergleichen. Neue Anwendungen können mit der cloudbasierten Plattform direkt auf alle Standorte skaliert werden. Ziel ist es, konkrete Dienste und Funktionen im Umfeld der Produktion und Logistik des Volkswagen Konzerns in Betrieb zu nehmen. Die Umsetzung des Gesamtprojekts ist auf mehrere Jahre ausgelegt. Volkswagen legt seine Industrial Cloud als offene Plattform an mit dem Ziel, Unternehmen aus der gesamten Wertschöpfungskette zu integrieren. Langfristig geht es um die Integration der globalen Lieferkette des Volkswagen Konzerns: über 30.000 Standorte von mehr als 1.500 Zulieferern und Partnerunternehmen. So entsteht ein stetig wachsendes, weltweites Ökosystem.
Umwelteffiziente Fertigung
Mit der Funktionalbereichsstrategie „Intelligent vernetzt“ planen wir die Produktion von morgen. Ressourceneinsatz und Emissionen der Standorte des Volkswagen Konzerns erfordern dabei besondere Aufmerksamkeit. Das Programm „goTOzero Impact Factory“ entwickelt konkrete Schritte zu einer nachhaltigeren Produktion. Die Vision ist eine Fabrik ohne negative Auswirkungen auf die Umwelt. Integraler Bestandteil des Programms sind die Themen Dekarbonisierung, Biodiversität und Zero Plastic Waste (Plastikvermeidung) in der Produktion.
Wir fördern weltweit die Vernetzung und den Austausch zwischen den Marken, um Synergien zu heben. Unsere Umweltexperten treffen sich regelmäßig in Arbeitsgruppen. Außerdem schulen wir Mitarbeiter zum Thema Umweltschutz.
In einem IT-gestützten System erfassen und katalogisieren wir Umweltmaßnahmen, die wir für einen konzernweiten Best-Practice-Austausch zur Verfügung stellen. Im Berichtsjahr wurden in diesem System rund 1.240 umgesetzte Maßnahmen im Bereich Umwelt und Energie dokumentiert, die der Verbesserung der Infrastruktur und der Produktionsprozesse von Pkw und leichten Nutzfahrzeugen dienen. Diese Aktivitäten lohnen sich in ökologischer und ökonomischer Hinsicht. Mit vielen effektiven und innovativen Maßnahmen wurde auch im Berichtsjahr wieder die Reduzierung der Umweltindikatoren vorangetrieben, die beispielsweise in den Dekarbonisierungsindex (DKI) einfließen, und zugleich Produktionsprozesse verbessert wurden.
GoTOzero Impact Logistics
Um zur Erreichung der Ziele des Konzern-Umweltleitbildes goTOzero in der Logistik beizutragen, arbeitet die Konzern-Logistik gemeinsam mit den Kollegen der Marken in der Initiative goTOzero Impact Logistics zusammen. Diese knüpft an die bisherige Initiative Green Logistics an. Durch die kontinuierliche Optimierung des Produktions- und Transportnetzwerks werden Emissionen reduziert. Darüber hinaus wird der Einsatz neuer, emissionsarmer Technologien im Transport von Produktionsmaterialien und Fahrzeugen geprüft und forciert.
Die vom Volkswagen Konzern ergriffenen Maßnahmen für eine CO2-neutrale Logistik umfassen die Verlagerung von Transporten von der Straße auf die Schiene und die CO2-Freistellung des Schienenverkehrs in Zusammenarbeit mit der Deutschen Bahn AG. Darüber hinaus stellt die Konzern-Logistik die weltweit ersten mit Flüssigerdgas (LNG) betriebenen Roll-on-Roll-off (RoRo)-Charterschiffe für den Fahrzeugtransport über den Nordatlantik in Dienst und setzt sich dafür ein, dass für Volkswagen fahrende Speditionen LNG-Lkw einsetzen.